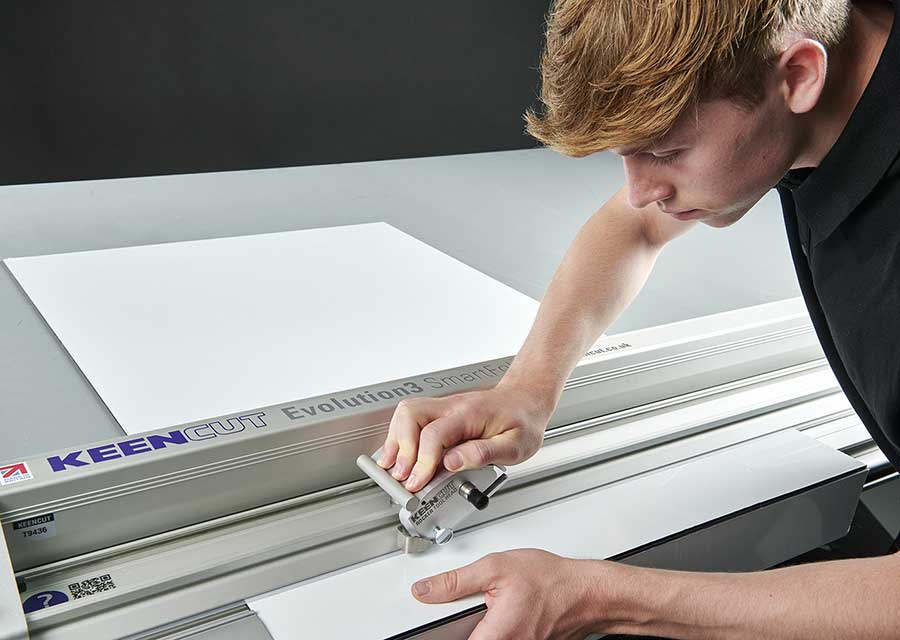
Scroll down to view the guide.
You can expand and collapse sections using the + and – icons.
View PDF version >
Register your cutter to activate your guarantee >
Visit Keencut support centre >
Visit user forum >
Installation video >
Contact Keencut >
This User Guide for the Evolution3 SmartFold gives advice on cutting techniques, using the different cutting heads and care and maintenance of your machine.
Before using your machine make sure that you have installed and calibrated it correctly. Full details are in the Installation Manual.
A material stop is mounted at both ends end of your SmartFold (seen highlighted in this image). When cutting tough or thick materials at prevents it sliding when being cut.
Insert your piece of material and lower the lift and hover so that it is just above the face of the material (as shown previously).
Butt the material up to the stop before clamping it in place.
The material stop can be rotated to move it out of the way.
Particularly useful when an clear work surface is required for other purposes.
The patented ‘Lift-and-Hover’ is a unique Keencut development that combines three features to give the ultimate in accuracy and productivity.
The SmartFold can hold the whole length of the cutter bar a very short distance above the object being trimmed and hold it there even if the levers are released. This leaves both hands free to align the objects cutting marks to the edge of the sightline strip. Pushing either lever fully lowers the cutter bar and clamps the object ready for cutting.
Hover action – See how to adjust the hover action >
Sightline strip – These are easily replaceable and are available from your supplier.
See how to replace the sightline strip >
The SmartFold includes an integral polymer cutting strip for use with the Evolution3 Fabric tool head to cut textiles and fragile materials. A simple push button at each end of the bar allows the cutter to be set on any of four cut lines, extending the life of the strip. There is no need for a separate cutting mat.
Pull and remove end stop.
Slide the cutting head to the right.
Lift up the head to remove it.
Insert the cutting head of your choice, and slide it to the left.
More than one tool can be mounted on the cutter bar if required.
Always replace the end stop.
Pull and remove end stop.
Slide the cutting head to the right.
Gently lift to remove the cutter head, then replace end stop.
Grip the cutter bar firmly, lift carefully and swing over the edge of the bench, bring gently to a stop when vertical.
Be careful when lifting |
Pull the lever to raise the cutter bar, place the material for cutting approximately in position under the cutter bar.
Push the lever to lower the cutter bar so it is only 1-2mm (1⁄16”) above the surface of the material, the closer to the material it is the less lining up error you will get when viewing the cut marks.
Look down vertically to align the edge of the sightline strip to the cut mark.
When fully aligned use the lever to lower the cutter bar onto the material and clamp it in position ready for cutting. Further cutting information is given in the sections under relevant tool heads.
See Double Graphik cutting techniques >
See the Fabric tool head cutting techniques >
QuikSwap Graphik tool head for Evolution3 cutters, with two individual blade holders for two way cutting. Graphik blades are stronger and more stable than regular blades. Ideal for vinyl, banner, cardboard, PVC foamboard up to 13mm (½″), foam-centred board, corrugated plastic, paper, pop-up and roll-up materials.
This head is supplied as standard with all Evolution3 cutters.
Undo the highlighted knob to remove the magnetic blade clamping plate.
Pull the magnetic blade clamping plate away from the cutting head.
Insert a Graphik blade, check it is facing the correct way for your desired direction of cutting. Place the small pin in the hole at the top of the blade and align with the edge of the clamping plate.
Replace the blade clamping plate onto the blade holder but do not tighten fully until the blade depth has been set (see how to adjust the blade depth >).
Repeat on the other blade holder if required.
The cutting head can be pulled or pushed to cut the material. Load and align the material to be cut as described in the ‘clamping material’ section (see how to align and clamp the material >), press down the chosen blade holder whilst pushing/pulling the cutting head along the cutter bar.
Tip: Only finger pressure is needed to hold the blade holder down, if after making the cut the blade holder has risen and the blade not cut through simply cut again. This could be an indication the material should be cut in two strokes using the dual blade depth setting as explained above.
Undo the highlighted knob to remove the magnetic blade clamping plate.
Pull the magnetic blade clamping plate away from the cutting head.
Lift off the blunt blade (if there is one) and replace with a new Graphik blade, check it is facing the correct way for your desired direction of cutting. Place the small pin in the hole at the top of the blade and align with the edge of the clamping plate.
Replace the blade clamping plate onto the blade holder but do not tighten fully until the blade depth has been set. Repeat on the other blade holder if required.
To adjust the height of the blade, loosen knob ‘A’ by a half to one full turn. Move knob ‘B’ up or down until the blade is long enough to just cut through the material.
Place a piece of the material under the cutter bar so it does not protrude past the edge of the cutter bar and the blade can be seen against the edge of the material.
Tighten ‘A’ to lock the blade in chosen position.
The design of the Graphik blade allows it to be set in the blade holder to cut in either direction. The cutting head can be used with both blades cutting in the same direction or in opposing direction.
The blades also have adjustable cutting depth, so if a thick material is being cut on a long machine such that it is beneficial to make two cuts, one blade can be set to cut half the thickness in one direction and the other to cut full depth on the return journey.
When cutting thick, tough materials such as PVC foam board and fluted plastics such as Correx or Coroplast, set the blade depth so the blade tip protrudes only 1-2mm (1⁄16”) through the thickness of the board and cuts from left to right.
Position the board against the right hand material stop and clamp in place.
Position the cutting head to start the cut, turn your body to face to the right and place the palm of your right hand on the cutting head.
Take a firm grip on the cutter bar with your left hand.
Depress the blade holder and push the cutting head using the strength across your shoulders.
Tip: If the material is too thick to reasonably cut in one stroke the blade can be lowered partially and the board cut in a number of strokes.
Cutting Aluminium Composite Panels is not recommended using the Graphik tool head.
Thin materials such as paper and plastic films are easily cut but attention should be given to supporting the material at the beginning of the cut. Pressing down lightly on the edge of the material with your index finger or thumb will prevent the material creasing when the blade starts cutting.
Check that the material is not being pushed into the cutting groove as the blade is cutting. If so, the material is likely to be suited to being cut with the rotary blade of the Fabric tool head where the underside of the material is supported on a plastic cutting strip. As a short term measure, it is possible to use the Graphik blade on the plastic cutting strip but too much use will quickly wear out the strip. Refer to the Fabric tool head for instruction to engage the cutting strip.
Scoring Acrylic and other plastics can be achieved by setting the blade at minimum depth and running the blade backwards across the surface whilst applying firm downward pressure on the blade holder.
Remove the material from the cutter for snapping by hand, some plastics may benefit from being scored multiple times.
When cutting a small piece of board place it at one end of the cutter and place a scrap piece at the other end to keep the cutter bar parallel to the base.
Loosen the clamping knob.
Remove the blade cover.
Remove the safety cover.
Remove the blade and magnetic blade boss. There may be a number of clear plastic shims on the threaded shaft, ensure they are clean and in good condition.
Separate the boss from the blade and inspect the boss for wear and clean off any debris. Dispose of the worn blade responsibly.
Reassemble with a new blade. Do not over tighten the clamping knob, it is essential that the blade is allowed to rotate whilst cutting.
Raise the cutter bar.
Press and hold down the highlighted button on the right side of the unit. Push the end of the cutter bar away from you.
There are four cutting positions on the strip numbered 1 to 4, align the edge of the aluminium end block approximately so the number 1 on the label is seen, release the button and move the top section backwards and forwards slowly until the button clicks into place. Repeat these steps on the other side of the unit.
Once track 1 has worn move onto tracks 2, 3 and 4 as required.
If all tracks are worn the strip can be turned over or see how to change the plastic cutting strip >
Turn the highlighted screw to adjust the blade pressure (clockwise to reduce). When adjusting you will see the pressure indicator go up and down.
Rotate the red blade guard, using tab (B), to reveal or hide the blade. If it is difficult to rotate loosen the clamping knob (A) a little. Ensure it is adjusted correctly before cutting so the blade is just able to rotate without sideways movement.
Take a small piece of the material to be cut, clamp it under the cutter bar.
The Fabric tool head cuts in both directions and requires the blade holder to be pressed down fully whilst the rotary blade is cutting the material.
Check the blade is rotating and not moving from side to side, if it is, adjust the blade clamping knob.
Cut in one smooth continuous motion, adjust to increase or decrease the cutting pressure if necessary.
When the small piece of material has been cut successfully place the main piece of fabric in the cutter, align and cut in the same way.
The three creasing wheels supplied with the Creaser tool head will each produce a different style of crease. Experiment on small samples of your material to see which gives best results.
Remove the lower clamping knob.
Remove the creasing wheel leaving the bearing and clear plastic shim in place.
Remove the upper clamping knob.
Choose the creasing wheel you would like to use and exchange it with the lower wheel. Replace both clamping knobs.
The Rocker tool head has been especially designed to give perfect comfort for all day, every day, cutting. The tool head fits the curve of your hand, allowing you to cut denser materials with ease.
The Rocker head accepts the Medium Duty blade and the specialist Tech D012 blade. This will allow you cut Aluminium Composite Panels (ACP) alongside standard materials.
To change the blade, loosen the blade clamping knob.
Remove the magnetic cartridge from the Rocker head.
Place the blade between the two guides, the magnet will hold it in place, and slide it back to touch the blade depth screw. The blade depth screw can be adjusted to set the blade correctly for the thickness of material to be cut.
Place the blade cartridge back into the cutting head, press on the end of the blade depth screw to ensure it is located fully in its slot and tighten the blade clamping knob.
When cutting thinner / less dense materials, ensure the blade depth is adjusted so only the tip of the blade is going through the material. Place your hand on the Rocker tool head as shown and rock it forward to engage the blade.
With the blade engaged, pull the Rocker tool head in one continuous motion along the material to achieve the best results.
If the material creases at the beginning of the cut use the index finger on your other hand to pinch the material onto the base plate and hold it in place whilst the blade enters the material.
When cutting thicker / more dense materials, ensure the blade depth is adjusted so the blade tip cuts 1-2mm (1⁄16) through the material. Place your hand on the Rocker tool head as shown, press down with your palm to engage the blade.
Push the Rocker tool head slowly through the material.
Extra effort can be applied by holding the grip area on the top of the cutter bar with your other hand and using the strength across your shoulders to push. Thicker materials can be cut in several passes.
The material should be in contact with the material stop to prevent it moving when cutting.
Use the Tech D012 blade and set the depth so the tip passes through the ACP by 1-2mm (1⁄16”).
Use the push technique to cut though the ACP, it usually takes 5-6 passes of the blade to cut all the way through and will require an amount of effort.
The finish should be clean but the edges may be sharp and require finishing with a file.
Alternatively, some ACP’s will snap once the top foil has been cut, bend back and forth a few times to break the bottom foil then clean the edges with a file.
Use a vacuum cleaner to remove any dust and smaller debris.
Frequency: daily as required
Moisten a cloth with diluted detergent to wipe down the cutter bar and base plate, dry with a cloth.
Frequency: weekly
DO NOT use solvents or aggressive cleaning products.
Put a small amount of petroleum jelly (Vaseline) on the scouring surface of a dish washing sponge and rub it up and down the two tracks. Wipe clean any surplus with a dry cloth.
Frequency:
Light use – monthly
Heavy use – weekly
When using the Fabric tool head with the purple plastic cutting strip, it will become scored and require replacing. Adjustment of the cutting pressure to keep it to a minimum for the fabric being cut will help to extend the life of the strip. Check you have used all four cutting tracks on the strip before proceeding.
Carefully fold the cutter bar over to reveal the base plate. This may require 2 people.
Be careful when lifting |
Both sides of the cutting strip can be used, it is important the strip is turned over in the correct orientation. The four tracks are offset to one side so when the strip is turned over correctly the new set of four tracks do not align with the originals.
The cutting strip is removed by sliding it to the right, to keep the orientation of the strip correct the left hand end should remain on the left once turned over.
There is a small adhesive patch under the left hand end of the strip to prevent it sliding in use, lift up the strip by sliding a flat edge under the left hand end of the strip and it should then slide to the right. A wide bladed flat screwdriver can be used to help push the strip.
Turn over and re-insert the cutting strip so that the smooth surface is now facing upwards and what was the left hand end goes in first. Push it in nearly all the way, again use a flat edge under the left hand end to raise the strip above the adhesive patch, when in position press the strip onto the patch to prevent it sliding.
Should the patch have lost its stickiness, peel it off and replace with a small piece of double-sided adhesive tape.
Once the strip has been fully used on both sides a new strip will be required, these are available from your dealer. Keencut part code EVOTCS
Tip: Order replacement strips (or check stock) whenever turning a strip over.
When using your SmartFold, the sightline strip may become scored or damaged.
To change the sightline strip, first grip the cutter bar firmly, lift carefully and swing over the edge of the bench, bring gently to a stop when vertical.
Be careful when lifting |
You will see the sightline strip on the underside of the cutter bar.
Remove the damaged sightline strip making sure that all residue from the adhesive tape is removed.
Your new sightline strip will have a protective backing on the double sided tape found on the underside of the part. Remove this backing.
Apply the sightline strip in stages from left to right, ensuring that no wrinkles or bubbles form under the tape.
Once you fold over your SmartFold, you will notice the sightline strip is larger than it needs to be. Use the Double Graphik tool head to gently cut the sightline strip.
Tip: it is recommended to do this in 3 passes to ensure that the line cut by the blade is as straight as possible.
Once you have removed the excess, your sightline strip will be configured to your machine giving 0.2mm of accuracy.
Tip: Order replacement strips (or check stock) when you notice any damage.